This spring in the Dutch port city of Rotterdam, cows will walk on water.
Holy cow?!
Well, not exactly: they’ll simply be the first offshore bovine residents aboard a maverick urban agtech project known as the Floating Farm.
Two vast steel mooring poles fasten a buoyant three-story structure of concrete, steel, and polycarbonates to the riverbed beneath Rotterdam’s Merwehaven Harbour.
If it is a bit surprising all those materials stay afloat, it will be even more so once it gets packed, over the next few months, with a hale and hearty herd of 40 Meuse-Rhine-Issel cows. And their 20 or so calves. All with enough heavily-automated robotic machinery to feed, milk, monitor and clean them — as well as a cluttering of milk processing plants and storage units below deck. There’ll even be various machines for making offshore yoghurt.
“No cheese here, though,” concedes Floating Farm co-founder Minke van Wingerden, speaking to AgFunderNews during an exclusive on-board tour.
A behind-the-scenes look ahead of the farm’s official curtain raiser shows the construction to be nearing completion but still some work to go. The launch has been postponed from Q4 2018 due to design and construction complications. (The exact date for its opening this spring has still not been set, either.)
But wait, how come no cheese? Better than floating cheesemakers or a sea-salted Edam, according to van Wingerden, is to use any spare space on board as classrooms for educational tours and a dairy shop.
“Too many people in cities today do not know where their food comes from, or how it gets made,” she says. A key aim of the farm is to show how food can be made locally, transparently, and in a financially viable way — while also respectful of animal welfare, climate adaptive and environmentally sustainable.
Perks from a low-carbon, locally-sourced supply chain, and agri-tourism are vital for keeping this project afloat. The farm has not received government or EU subsidies. So it is competing for market space within an already huge (and often subsidised) Dutch dairy industry on land. The founders estimate their cows will produce a combined 800 liters of milk per day, which may sound like quite a bit. But it is a relative drop in the ocean when set against combined production nationally. The Netherlands is already a heavyweight dairy exporter priding itself on high yields and well-regulated production — and in 2017, the Dutch dairy industry processed 14.1 billion kilograms of milk products. That was all after the culling of over 100,000 cows across the country as a result of strict EU quotas on phosphate emissions.
Udderly Brilliant, or Mad Cow-Culations?
Besides, previous offshore urban farm ideas have long been hampered — and scoffed at — because building and operating anything, let alone entire cow farms, along a busy city’s waterfront requires costly and ingenious design plans. Then by high construction, maintenance, and insurance costs. And that is to say nothing of a complex regulatory minefield to navigate. Fair enough for offshore wind or fish farms, maybe. But for cows? Such hoopla in return for lower volumes than on land — which is, surely, a more natural and spacious bovine habitat. For that matter, won’t cows get seasick offshore?
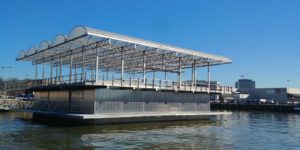
And yet, projects like Rotterdam’s Floating Farm might upend some of these timeworn assumptions. Global trends like advancing technology, and rising populations and sea levels allow for offshore cow farming to make its maverick case. On the nearby shore, where the Floating Farm cows can reach a small patch of fresh grazing pasture via a jetty, there are signs of a few interesting long-term advantages for this herd and their ambitiously amphibious farmers. Not far beyond the surrounding docklands are local beer breweries producing off-spill that otherwise goes to waste but is a cheap and nutritious meal for cows. The same goes for the grass from nearby golf courses and football pitches, which are set to receive local manure in return.
And the docklands themselves offer a few promising signs. The wharves and shipping containers of Merwehaven are undergoing a vast urban reboot. The farm is being promoted by urban planners as a creative way to fill the void left by ships that now dock elsewhere. (The hulls of larger ships calling in at Rotterdam, Europe’s largest port city, are too big and deep for Merwehaven these days). Luxury flats and co-working spaces are springing up as part of the reinvention. Why not offshore farms too?
One such trendy co-working space is used by the Dutch property company Beladon, which runs and owns the Floating Farm. The company is backed by private investors and a bank loan, the nature of which founders declined to specify. Around 10 employees are working on the farm, as well as on experiments with LED-grown lettuce in a nearby shipping container. If it all works out with cows, then chickens, pigs or vegetables could well be next, and surely a fair bit easier.
Standing at a balcony with sweeping views across Rotterdam, Beladon CEO Peter van Wingerden raises one other advantage. “It’s climate adaptive,” he says, looking out across the Rotterdam cityscape.
Roughly 90% of Rotterdam sits below sea level, a worrying predicament in the context of melting ice caps and rising oceans due to climate shifts. Farming land across the Netherlands is similarly vulnerable, with much of it having been reclaimed from the sea. The floating farm, as the name suggests, rises and falls with the tides.
Minke Van Wingerden, who is Peter’s wife as well as his business partner, says the idea came to her husband in 2012 during Hurricane Sandy. He had realised then and there how useful floating structures could be in natural disaster relief operations, especially if vital infrastructure gets damaged by flooding, earthquakes or hurricanes. Seven years down the line, he is on the brink of achieving a pilot design that could be replicated round the world.
“At first I thought it was a silly idea,” says Minke, “then I realised it was brilliant… So many of our cities sit by ports, and it is time we started to use our waterways with more intelligence and creativity.”
The architecture firm tasked with mapping out this pioneering dream is Goldsmith. Wesley Leeman, a partner at Goldsmith, says bringing this into reality required overcoming all sorts of “dogma” left over from best practices relating to horizontal farming on land.
Thinking about urban and aquatic surroundings, as well as with robotics and vertical farming, were all a challenge, he admits: “This was a tough nut to crack,” he writes in an emailed exchange from his office in Rotterdam. “It required a large number of new solutions on almost all scale levels of the design.”
Now, however, the idea of offshore farming is “exploding out from under us,” he says by phone, noting how he was now at work designing other pioneering offshore farming structures, such as those for chickens and vegetables.
Moo-ving with the tides
Back in the Floating Farm HQ, meanwhile, a young and relaxed Albert Boersen awaits the arrival of his new herd.
Boersen hails from a family of farmers, and is a new generation is every sense: like so many millions in rural areas around the world, he has moved from the countryside to the city and is as much a data scientist as a manual labourer.
“I did the same thing that a lot of people do — except now I get to keep farming,” he says.
Deciding which cows should go offshore was tough, he said. There had been a French breed lined up, but it was ultimately vetoed on the grounds of patriotism in favour of a Dutch one. It will also be an all-female herd on board, for reasons of safety.
“There’ll be no bulls,” he says flatly. “It was a hard choice, but we decided to use AI — Artificial Insemination.”
There’ll be plenty of Artificial Intelligence, too. Instead of the cows relying on human working hours for milking times, they will learn how to get themselves milked whenever they want. Just step into a robotic milk parlour designed by robotic dairy leader Lely, which tracks and analyses the milk quality, consistency, and quantity in relation to their nutrition that day.
“I know everything about these cows, without having to interfere,” he says, adding that he can check on his herd’s health and output from anywhere in the world via a tablet or smartphone, allowing him to spend more time thinking about specific dietary or medical requirements for each cow. “I think animal welfare is the most important thing to do here.”
Neither does he see the manual approach with rose tinted glasses. “My father is 59 now. His shoulders are gone.”