[Disclosure: AgFunder—the parent company of AgFunderNews—is an investor in Modern Synthesis]
Biomaterials startup Modern Synthesis and Danish fashion brand GANNI have teamed up to create GANNI’s signature ‘Bou Bag’ using a leather-alternative produced, in part, by bacteria.
The bag—on display this week at the London Design Festival—should be commercially available by early 2025, says GANNI, which is working with a series of startups developing materials with a lower environmental impact as part of its Fabrics of the Future program.
Created with nanocellulose derived from bacterial fermentation, the ‘biotextile’ is designed as an alternative to animal- and petroleum-derived materials, said GANNI, which has committed to phasing out virgin leather from its products.
Modern Synthesis CEO Jen Keane said: “Collaborating with GANNI on the Bou Bag has allowed us to showcase the viability of bacterial cellulose-based materials in real-world applications. These one-off showcase pieces are pivotal in evaluating a material’s workability and appeal to both designers and consumers, which paves the way for its eventual integration into everyday fashion.”
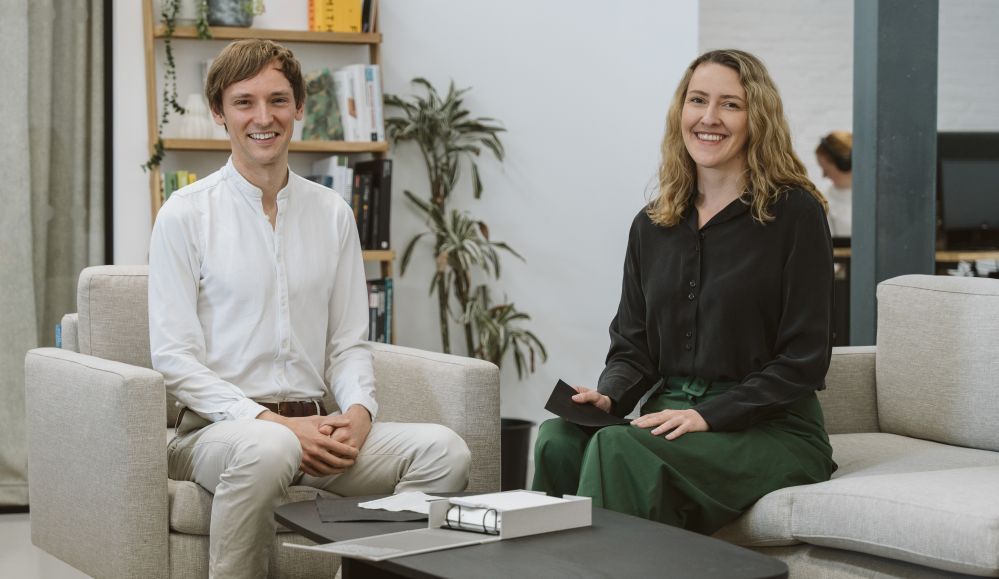
Lightweight but strong
Founded by ex-Adidas designer Jen Keane (CEO) and synthetic biologist Dr. Ben Reeve (CTO), London-based Modern Synthesis raised $4.1 million in seed funding last year and joins a growing number of startups in the biomaterials field, from Ecovative to Bucha Bio, MycoWorks [another AgFunder portfolio company], and Bolt Threads, which recently paused production of its mycelium-based leather indefinitely citing challenging market conditions.
Modern Synthesis’ patent-pending process creates a customizable biomaterial in roughly 10 to 14 days. The startup—which opened a pilot facility in London last year—first creates a scaffold made from other natural fibers such as hemp or linen, around which the nanocellulose can form, creating lightweight but remarkably strong materials, Keane told AgFunderNews.
“We use a natural textile scaffold that reinforces the nanofiber matrix – similar to how rebar is used to reinforce concrete. We use cellulosic fibers such as hemp, linen or lyocell. Research supports that cellulosic materials are safely biodegradable at the end of life, and have the potential to be recycled depending on the desired use-case. The textile scaffold also enables a huge range of flexibility in the final material’s look and feel. The resulting textile can be processed on the same equipment as conventional textiles and naturally-derived coatings can be added for additional functionality.”
Keane added: “The bacteria we work with consume agricultural sugars and produce a fiber called bacterial nanocellulose as a natural byproduct of digestion. Because the bacteria are feedstock agnostic, these sugars can be sourced from a variety of agricultural waste streams, enabling de-risked and decentralized supply chains.
“Through our patent-pending process, we are uniquely able to form the nanocellulose biofilm around the textile scaffold to create a finished material. Unlike other cellulosics, which grow in fields over months or years, our bacterial nanocellulose can be grown in bioreactors in days, with very few inputs.”
A tunable process
Asked how tunable the process is, she said: “We can genetically modify the bacteria to create new functional properties, as we’ve demonstrated in collaboration with Imperial College.
“However, genetic modification is not required to unlock customization; we’ve developed an end-to-end process that enables us to ‘tune’ the material to meet specific brand requirements. So we can, for instance, manipulate the flexibility, thickness and functionality of our material by adjusting the concentration of nanocellulose fibers. We can also make tailored tweaks in the post-processing process with natural additives and finishes.
“From a textile perspective, when we alter the yarn composition or patterning in the natural textile scaffold, we can deliberately change the hand feel, texture, and types of product forms which are possible.”
Sponsored
International Fresh Produce Association launches year 3 of its produce accelerator