A major blocker today for the electrification of the greenhouse is energy — specifically, access to renewable energy that would bring operating costs down and help decarbonize the sector.
Switzerland-based Voltiris believes spectral filtering is the key to helping growers accelerate their energy transition and gain profitability in the process.
The company uses these spectral filters to separate sunlight into two components. Wavelengths essential for plant growth are allowed to pass through, while unused light gets redirected onto high-efficiency solar cells. Cells then convert sunlight to electricity that can power the greenhouse.
“Currently, our value proposition resides in the clean energy we provide,” Nicolas Weber, CEO and cofounder of Voltiris, recently told AgFunderNews.
At the same time, “We’ve observed some very interesting preliminary agronomical results,” he adds. “By filtering light, we remove specific wavelengths that usually harm or stress crops. This improves the greenhouse climate significantly, getting growers very excited.”
Below, Weber discusses the origins of Voltiris, how spectral filtering works, and the use cases for it beyond the greenhouse.
AgFunderNews (AFN): How did Voltiris come about?
Nicolas Weber (NW): I was fortunate to meet Jonas [Roch, CTO], one of my co-founders, in high school nearly 20 years ago. He was always gifted in physics, and we often talked about building something together.
Fast forward a few years, I had spent almost six years working at the Boston Consulting Group, gaining entrepreneurial experience and spending time on sustainability topics, including reducing Scope 3 emissions for retailers. Ultimately, after becoming a father, I felt a strong desire to take on a more hands-on role in addressing the climate crisis and advancing the energy transition.
While having those internal reflections about sustainability, Jonas came to me with the idea behind Voltiris. He said, “Hey, I have this idea about working with light, specifically splitting light to provide crops what they need for photosynthesis and using the rest to make energy.”
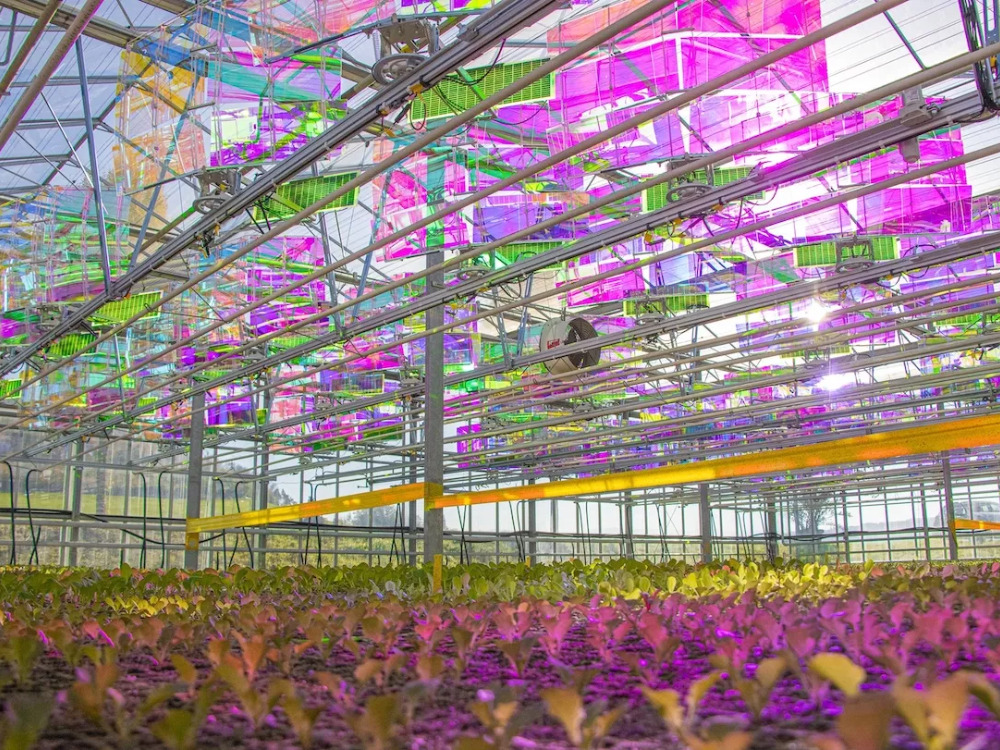
AFN: What is the motivating force behind the company?
NW: Our solution is at the intersection of food security and the energy transition, not only allowing growers to become more resilient and profitable but also accelerating their adoption of renewable energy. This is an extremely powerful driver.
We see that growers want to become more independent, more resilient, and at the same time incorporate more renewable energy into their greenhouses. One of the big blockers for electrification today is access to renewable energy.
What we do is open the possibility to transform the entire greenhouse into a solar field. We can tap into a surface that was previously unavailable to combine crop production with energy generation without compromising crop yield. In doing this, we secure access to a source of energy that is clean, independent, and cheaper than other alternatives.
The main blocker for electrifying greenhouse equipment — for example, heat pumps or even batteries — is access to a reliable source of electricity. By addressing this challenge and providing a critical piece of the electrification puzzle, we aim to become the platform that enables full electrification and decarbonization of greenhouses.
AFN: Tell us more about the problem Voltiris’ tech addresses.
NW: In talking to people in the greenhouse space we found out that greenhouse operators are extremely challenged by the energy transition. They currently rely heavily on fossil fuels, the cost of which has increased significantly over the years. Throw in the high price volatility into the mix and this puts the greenhouses business at risk.
There are a lot of questions about business continuity. When gas prices went through the roof two years ago, some 30% of greenhouses in the Netherlands stopped operations.
At the same time, there are increasing demands for greater sustainability along the supply chain. For example, MIGROS, the largest retailer chain in Switzerland, now requires greenhouse operators to be powered by renewable energy from 2026. I’m convinced that similar requirements will be raised across Europe and other parts of the developed world. If it is not retailers aiming to reduce their Scope 3 emissions, it will be governments or consumers requiring greenhouses to transition their energy sources.
This energy transition is not easy for greenhouse operators. They lack solutions for adopting solar energy at scale. Space for PV [photovoltaic technology] is often limited to the roofs of administrative buildings, yielding a lot less energy than what they need. In Europe in particular, there is seldom any space next to their greenhouses and, even if there is, obtaining PV building permits can take years. On the other hand, installing solar panels directly on top of the greenhouse is not an option for such solutions shade crops reducing the amount of light that comes in, which in turn eats into crop yields.
Our solution is based on spectral filtering and extremely differentiated for greenhouses. At the same time, since we install our solution inside the greenhouse, we don’t require permits to deploy solar projects. This means we can very quickly help growers gain independence, profitability, and accelerate their energy transition.
AFN: How does the technology work?
NW: We make use of the full light spectrum by addressing the unique needs of plants while harvesting and converting the rest into solar energy.
Plants require only specific wavelengths of sunlight for photosynthesis, leaving a portion of the light spectrum unused. Voltiris utilizes spectral filters to separate sunlight into its components: the wavelengths essential for plant growth pass through unaffected, while the unused light is redirected and concentrated onto small, high-efficiency solar cells. These cells convert the excess sunlight into electricity, effectively enabling a sustainable, dual-purpose use of the same land for both agriculture and energy generation.
Installed inside glass greenhouses, between the crops and the roof, our modules use proprietary solar trackers to ensure optimal reflection onto the solar cells, extending the solar energy generation throughout the day.
The solution is designed to ensure seamless installation and smooth operation. It can be retrofitted into existing greenhouses without the need to shut down operation during the installation. Again, it does not require building permits for deployment, which ensures a faster rollout — a critical advantage when it comes to agrivoltaics.
We’ve also observed another significant benefit: the Voltiris spectral filtration helps keep crops cooler during the hot summer months, providing shade while still allowing all the light plants need for optimal growth.
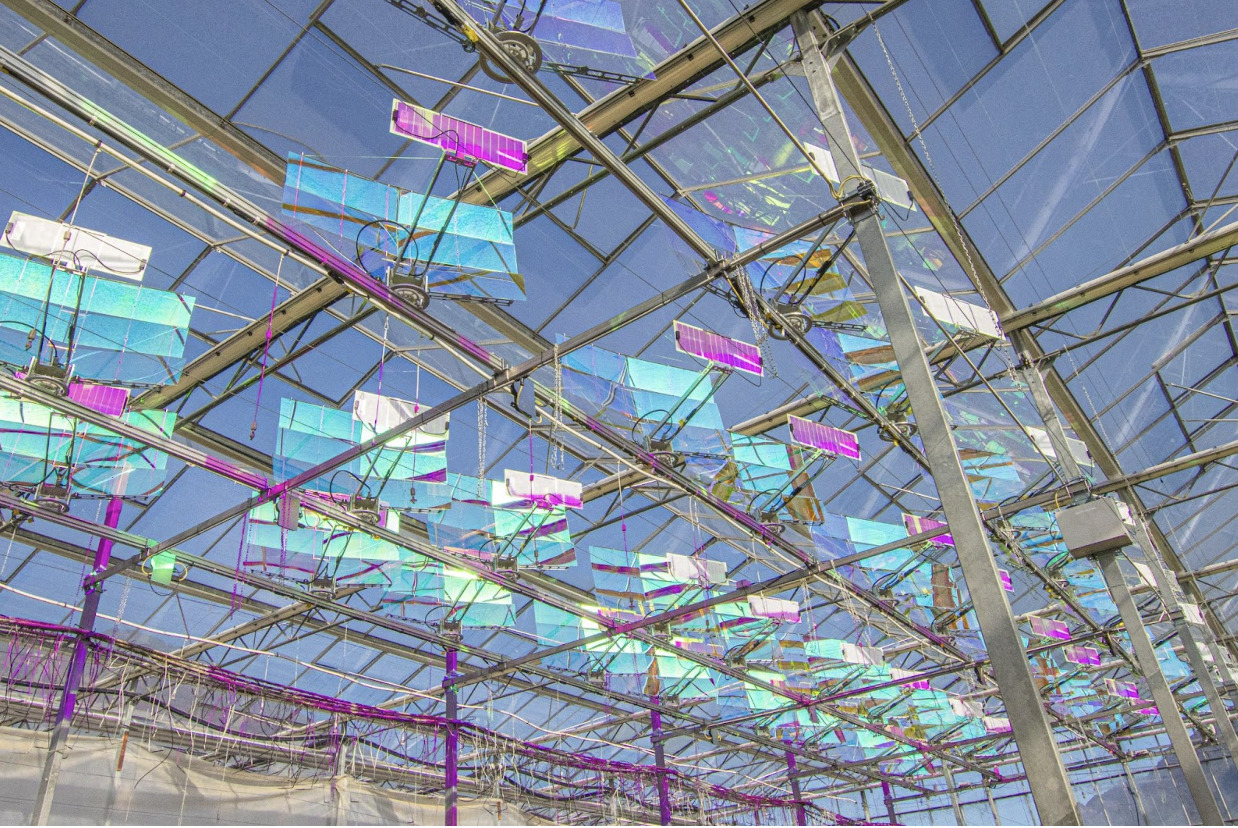
AFN: Could the tech work in other settings besides greenhouses?
NW: Great question. Indeed, this concept isn’t limited to high-tech greenhouses; it could have various applications with different product designs tailored to other settings.
For example, our approach could be adapted for plastic greenhouses and also to outdoor crops, both of which we’ve already started exploring. You could also imagine extending the applications beyond crops, such as fish farming or buildings.
Yet, we need to walk before we run. Given the urgent need for solutions in high-tech greenhouses, we have made a conscious choice to focus here first. The opportunity for impact, creating value to growers, increasing food security and resilience is much greater in this segment of agriculture—for now.
AFN: How does your technology differ from, say, LEDs typically seen in vertical farms?
NW: The similarities between our technology and LEDs used in vertical farms lie in the tuning of light for crops. In indoor farming, LEDs typically provide only specific parts of the light spectrum. For instance, indoor farms often use pink light, meaning only part of the spectrum is transmitted to crops.
However, with LEDs, the final light formula is additive: the desired “recipe” of light is created from scratch within a closed environment. In our case, we borrow some principles from indoor farms by providing crops with a specific part of the spectrum. But beyond the fact that our solution does not emit light and instead generates energy, there are three key differences:
- Subtractive light recipe: We take the full spectrum of sunlight and selectively filter out specific spectral bands to provide to crops.
- Outdoor operation: Unlike indoor farms, there is plenty of indirect light reaching the crops in our setup.
- Dynamic application: As our solution rotates throughout the day, the spectral filtration is applied to crops only for a limited portion of the day. Crops still receive other parts of the light spectrum during the day, just not to the same extent.
Interestingly, we’re now testing the compatibility of our solution with LEDs in some of our projects. Since we install some light infrastructure within the greenhouse to deploy our solution, LEDs can be installed right underneath, creating opportunities for combined approaches in outdoor greenhouses.
AFN: Where is the company currently at in terms of growth?
NW: We have now checked boxes across the agronomic, energetic, and scaling dimensions—the main elements necessary for adoption.
From an agronomical perspective, we’ve demonstrated that our solution works. We’ve conducted 18 projects in different regions and on various crops, collaborating with both research centers and key opinion leaders. For instance, we’ve worked with tomatoes in the Netherlands and Switzerland, peppers and flowers in the Netherlands, cucumbers in France, and blueberries in Spain. As a result, we now have strong buy-in from scores of growers confident that our technology will not affect crops negatively.
On the energy side, we’ve established how much energy our solution can produce across various setups and types of greenhouses. This process has provided significant insights into what drives the performance of solar units in greenhouse environments. Very importantly, we’ve developed robust internal models that allow us to predict with high accuracy how much energy we can generate for any type of greenhouse anywhere in the world.
Scaling operations is another critical dimension. It’s one thing to produce and install 10 solar modules; it’s an entirely different challenge to scale up to thousands. As the size of installations grows, the focus shifts from individual units to managing entire systems. Ensuring that these systems can be effectively controlled is a key component of scaling.
To support this scaling effort, we’ve deployed two large installations with utility players in Switzerland, establishing significant operational capacity. We’re now initiating our commercial rollout, starting with a one-hectare-scale installation in Switzerland. Concurrently, we’re conducting 10 projects with key opinion leaders, including Division Q, the innovation arm of Koppert Cress, in the Netherlands, Switzerland, France, and Belgium. We’re also running agronomical tests in the U.S., with additional tests being prepared in Canada and the Middle East. These projects are paving the way for our scaleup in the second half of next year.
Currently, our value proposition resides in the clean energy we provide. At the same time, we’ve observed some very interesting preliminary agronomical results. By filtering light, we remove specific wavelengths that usually harm or stress crops. This improves the greenhouse climate significantly, getting growers very excited. We are just getting started on this front.
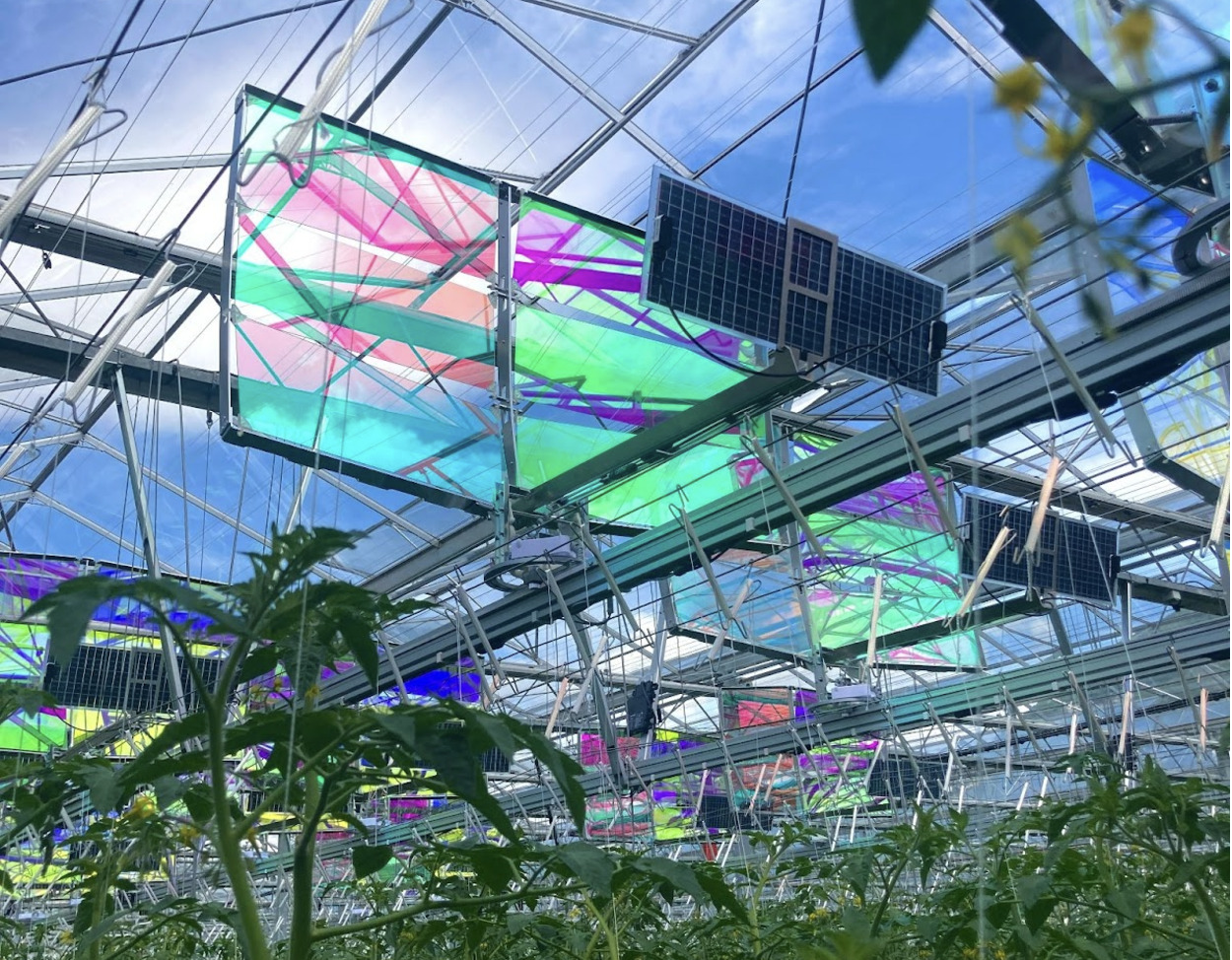
AFN: What is next?
NW: We’re at a tipping point. As one of the only, if not the only, company worldwide capable of executing solar projects within high-tech greenhouses, particularly for crops like tomatoes, cucumbers, peppers, and salads, we enjoy a unique position in the industry. The combination of proprietary technology, partnerships with growers and ecosystem leaders, and specialized in-house expertise allows us to make a significant impact on the greenhouse sector. Our vision is to transform the industry by integrating our solar units into every greenhouse, paving the way for carbon-free greenhouse production.
To achieve this ambitious goal, our two-year roadmap focuses on building further validation through projects with key opinion leaders and early adopters, initiating our commercial rollout across Europe while preparing for expansion into North America and the Middle East. We’re also investing in industrialization and scalability, not only through production tools but also by optimizing installation processes. To accelerate adoption, we are partnering with key ecosystem players, including greenhouse builders and climate computer providers.
At the same time, we are mindful of the need to carefully manage the pace of deployment. While we aim to create impact as quickly as possible, it is equally important to deeply understand growers’ needs, build trust, and avoid the risks of moving too fast or making (too many) preventable mistakes. Striking the right balance between speed and precision is essential to ensuring our solution delivers sustainable, long-term value.
Aligned with this strategy, we are actively seeking collaborations with innovative growers worldwide who share our vision, allowing us to further enhance our understanding and adapt to local specificities.
Sponsored
Sponsored post: The innovator’s dilemma: why agbioscience innovation must focus on the farmer first