Bulgarian insect ag startup Nasekomo is gearing up to launch a neonate delivery service for black soldier fly neonates that puts the tiny larvae in a state of suspended animation for up to 10 days without refrigeration, enabling insect farmers to focus on rearing and processing.
Upon arrival at an insect protein production facility, the “paused” larvae can be reactivated with a 95% recovery rate by placing them on feedstock and go on to “demonstrate superior growth performance and efficiency vs non-suspended neonates,” CEO Marc Bolard told AgFunderNews.
“The method eliminates the need for low-temperature storage during transit, reducing logistical complexities and ensuring a consistent, stable supply of larvae for producers.”
Nasekomo, which has a joint venture with French animal genetics expert Groupe Grimaud called Fly Genetics, leverages advanced genetic selection techniques to produce larvae with superior growth rates, feed conversion efficiency, and resilience, claimed Bolard. “These traits provide a competitive edge, enabling producers to achieve higher yields and more sustainable operations compared to other market players.
Starting in September, Nasekomo will expand its neonate delivery service through an online portal enabling insect farmers to order baby larvae, including the suspended variety, said Bolard.
“Our genetically superior neonates, supported by the innovative Fly Genetics program and our advanced suspension technology, provide a significant edge in growth performance and efficiency. This ensures that producers using our neonates achieve higher yields and better sustainability.”
Inducing suspended animation
So how are the larvae induced into a state of effective hibernation?
Like Israel startup FreezeM, which also ships “paused” neonates to insect farmers and processors, Nasekomo starts by placing them on an undisclosed substrate.
According to Bolard: “While the substrate content plays a significant role and represents a major innovation on our part, it’s the entire set of conditions ranging from the environment in which the neonates are laid and hatched to the packaging process.
“Our R&D efforts have focused on creating an optimal combination of these factors, enabling us to slow down the larvae’s metabolism effectively.”
He added: “We have sent neonates to almost 100 different customers and we are thrilled with the positive response and interest. Our aim is to expand delivery to a diverse range of companies involved in insect protein production, aquaculture feed, and other sustainable food and agricultural sectors.”
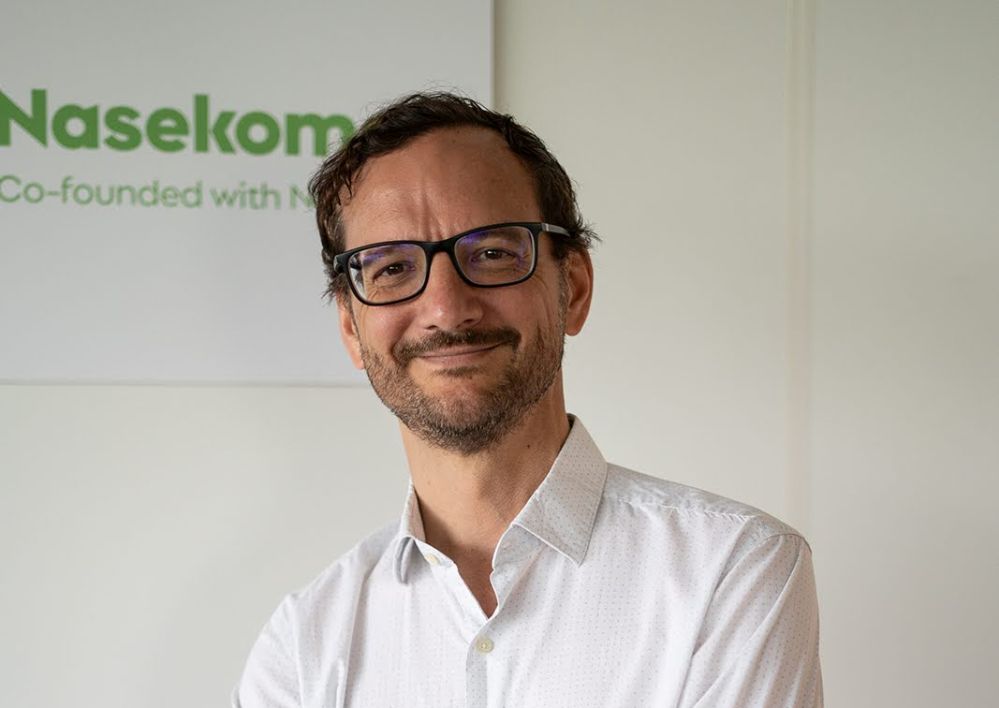
Insect farming at scale must be ‘automated and data-driven’
Insect farming at scale “has to be automated and has to be data-driven,” claims Bolard, who is working with tech giant Siemens to create a standardized insect bioconversion system.
Nasekomo has a demo facility in Bulgaria to showcase its tech and produce small quantities of product, but does not plan to own and operate its own facilities going forward, with Bolard arguing that a franchise model is the fastest way to scale the tech.
Its first (undisclosed) franchise partner, “a green investor,” will open a facility in Bulgaria in 2025, adds Bolard, who says his larvae can feed on a variety of industrial side streams from rice and wheat bran to brewers’ spent grains.
“As a franchisor, we’re an enabler who will deliver our franchisees everything they need to develop and run their operations, from the young insects to the insect building and equipment, to a patented solution to run the bioconversion process with AI algorithms that monitor, alert and improve the process in real time.”
Ideally the franchisee would locate facilities as close as possible to a consistent source of feed such as a food processing facility, says Bolard. But it does not necessarily follow that franchisees will typically be food processors looking to valorize their waste/side streams.
“Most food and beverage companies don’t want to lose focus [by trying to run an insect farming operation on top of the core food business], but they are willing to sign a long-term supply agreement [to provide a feed source to an insect farming facility located nearby].
“So we also need partners that want to develop the bioconversion business and help build a circular economy,” he says. “We’re talking to green investors but also waste processors and waste managers who are ready to invest along with food and beverage suppliers. Another quite different profile of partners is agricultural conglomerates that are in areas such as pig or poultry production.”
Further reading:
Sponsored
Sponsored post: The innovator’s dilemma: why agbioscience innovation must focus on the farmer first