High-tech insect farmer Oberland Agriscience aims to reach full capacity—3,500t of dry black soldier fly larvae (BSFL) protein and 9,000t of frass—at its new facility in Halifax next year after netting a loan from Peritus Capital.
“The equipment is arriving and being installed, and within the next two months, we are going to be producing protein,” founder Dr. Greg Wanger told AgFunderNews. “The goal is to be at full capacity [at the 108,000sq ft facility] within 2025.”
He added: “Nova Scotia is a wonderful place to start a company. We also have access to a lot of non-dilutive funding and I don’t think we would have got as far and as fast without a lot of that. The last couple of years were tremendously difficult [for agrifoodtech financing]; the taps dried off for everyone. But it seems now that things are starting to change. Look at our colleagues at [fellow Canadian insect farmer] Entosystem. They just raised CAD58 million ($42 million).
“People look at some of the companies in the insect ag space and say, ‘Where did all the money go?’ But the pioneers in the space really blazed the trail, particularly on the regulatory side [to get insect products approved for animal feed and petfood].”
The second wave of companies such as Oberland can build on their learnings and scale up “for orders of magnitude less,” he claimed.
“While many companies boast of having ‘rocket scientists’ at the helm, Greg Wanger truly brings that expertise—he’s a former NASA Jet Propulsion Labs scientist, and his rigorous training is evident in Oberland’s meticulous approach. Over seven years, they progressed from a pilot program to a full-scale commercial facility, continually testing, refining, and learning from industry challenges. This commitment to precision and resilience is why we’re so confident in their success.” Howard Tang, CEO, Peritus Capital
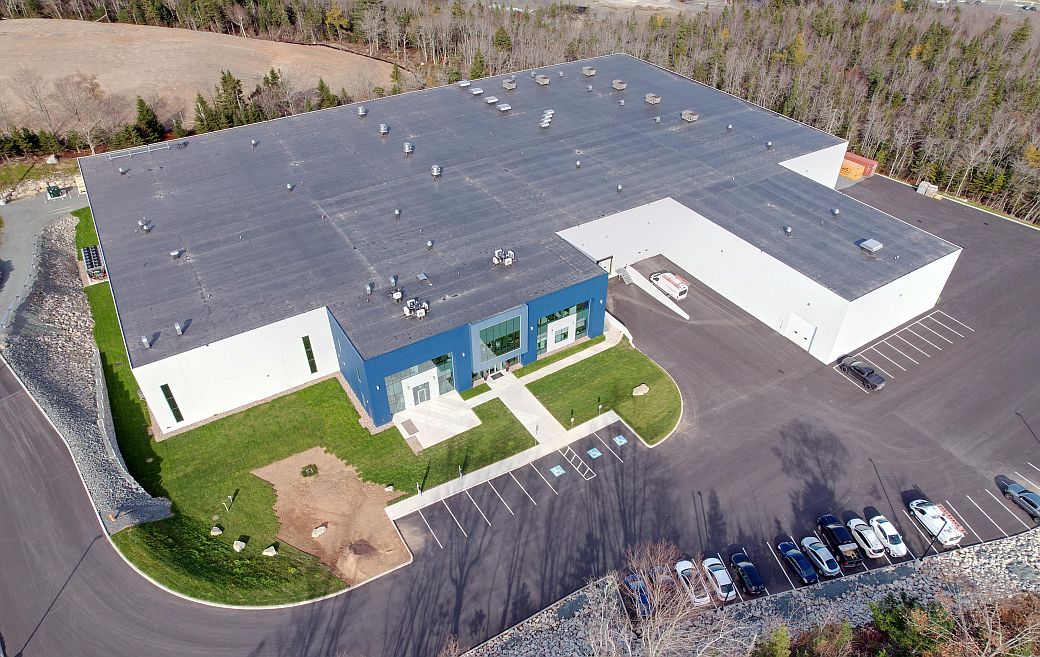
Funding rounds in insect agriculture, 2024 (US dollars):
- Entosystem (black soldier flies, Canada): $42 million
- Protix (black soldier flies, Netherlands): $40 million
- Tebrio (mealworms, Spain): $32.6 million
- FreezeM (black soldier fly neonates for breeding, Israel): $14.2 million
- Nasekomo (insect ag franchisor, black soldier fly neonate supplier, Bulgaria): $8.7 million
- Entocycle (enabling tech for insect ag, UK): $2.6 million
Source: Preliminary AgFunder data [disclosure: AgFunder is the parent company of AgFunderNews)
‘You really have to sweat the small stuff’
The key to success for insect farming is ironing out problems at small scale before you end up spending huge sums on scaling something that won’t work, he said. “One of the things that I learned in scale up projects coming out of the NASA Jet Propulsion Lab [where he worked from 2015-2018 before getting into BSFL production] is you really have to sweat the small stuff or something that you totally take for granted will come back to really crush you later on.
“So it’s simple things like the fact that water is heavy. When you’re in a lab and you’re moving a test tube around, you don’t even think about it. When you scale up, you need to know that water weighs a ton for every 1,000 liters, or these kind of things can really come back to haunt you.
“You have to be able to set aside things that sound like good ideas but are not scalable, and not spend a lot of time and effort chasing all these shiny balls that may sound great now, but when you do it 10 times bigger, it just isn’t going to work.”
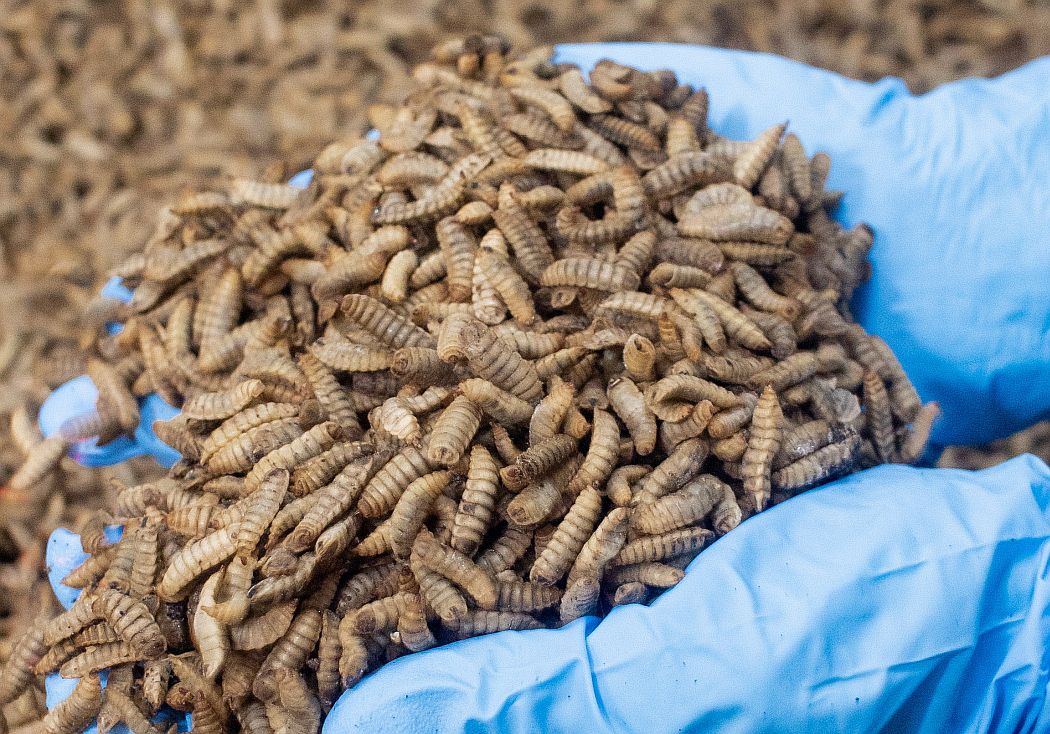
Feedstocks
When it comes to feedstocks, he said, black soldier flies “will eat just about anything.” But to get BSFL protein approved for feed or food, in many markets, you’re limited to using pre-consumer organic waste and byproducts that come out of the back of a processing facility, brewery, or the back of a grocery store, rather than household waste, for example.
“There is still variability in that feedstock, so we blend it to make the optimal mix, but we have to do some upstream processing [before it can be fed to the BSF larvae]. We also have to watch for any potential pathogens coming in, as look what happened in the cricket industry [which has been hit by various viruses over the years].”
There are some pathogens that could cause problems for black soldier flies, but “they are pretty robust, he said, “In fact, they produce a lot of interesting anti-microbials because they live in decaying matter out in nature. There are other soldier fly companies that are bio prospecting these and we’ve got some projects there too.”
“Black soldier fly larvae are a tremendous insect, capable of transforming almost any organic matter into a valuable protein with almost unrivaled efficiency.” Dr. Greg Wanger, founder and CEO, Oberland Agriscience
Vertical integration
Like Entosystem cofounder Cédric Provost, Wanger believes the insect ag industry may ultimately separate breeding from farming from processing. But right now, he said, it feels risky to outsource breeding, exciting though some companies in this space might appear.
“We can order some neonates, but I’m not willing to take that risk right now to say we won’t have the entire life cycle under one roof. But in future, I’d love to see multiple different ways of doing this.”
Unit economics
Looking at the unit economics of large-scale insect farming, costs have come down a lot in part due to automation, said Wanger, who is also using machine learning and predictive analytics to optimize production. “80 to 90% of our entire process is automated, and the remaining 10-20% could be automated. If you’re moving bins and trays around, there’s no need for a human to be involved other than to support and to monitor.”
But to succeed, it has to offer added value over existing protein options in food and feed, be on health, palatability, or the environment.
The feed market will accept a premium over say soy or fishmeal if there are environmental and health benefits, he said, “But not if it’s 10 times the price of the next competitor. The biggest shift for the insect industry in the past few years has been the [interest from the] pet food industry. A, it’s enormous, and B, given some of the margins, companies are willing to pay a little bit more for protein, particularly sustainable protein.
“We also some really big and interesting partnerships coming out of the poultry industry. If you’re talking about a direct replacement, it’s very tough to compete against soy. But there are anti-inflammatory and anti-microbial benefits to the animals and growth benefits that you get with using the soldier fly. And if feed companies are able to remove or reduce some of those other compounds and components in the feed [by using BSFL], the economics start to add up.
“And then finally, there are some salmon operations that we’re working with that are willing to pay a bit more because of the value we bring on the nutrition side, as well as on the carbon footprint side.”
He added: “If you look at the inclusion rates of fishmeal in salmon diets, it has gone down and been replaced with soy and other terrestrial based protein sources. But that brings along with it some challenges such as gastrointestinal issues. And the data out there and our research has shown that replacing [fishmeal with] soldier flies, you maintain good gut health and good growth in the fish.”
Further reading: