Coastal shrimp farming comes with a laundry list of problems, from slave labor and the destruction of mangrove forests and wetlands, to the pollution of waterways with organic waste, chemicals and antibiotics. It is also vulnerable to disease and extreme weather, prompting a flurry of startups to explore alternative approaches in recent years.
But while shrimp grown in recirculating aquaculture systems (closed systems whereby water is recirculated with waste products from the shrimp filtered out or/and processed by biological systems such as seaweed or/and microbes) can command a higher price, these facilities can also be extremely costly to build and run.
So how do you design a system that can eliminate the externalities that threaten coastal systems (primarily extreme weather and disease) and still make a margin?
AgFunderNews (AFN) caught up with John Diener (JD) cofounder and CEO at Singapore-based startup Vertical Oceans, to find out.
AFN: How did you get interested in shrimp farming?
JD: The original idea for Vertical Oceans came up when I was running the Gold Coin Aqua Nutrition business. I was visiting hundreds of shrimp farms and I kept seeing the same things; it didn’t seem like it was a very efficient system. I have this obsession with efficiency and I started thinking in the back of my mind, how would you solve this? How would you make this more efficient and make this a better system?
My time at Gold Coin was fundamental because I got to understand the aquaculture industry, which is incredibly complex because so many different disciplines are involved. There’s biology, there’s chemistry, microbiology, hardware… and I’m drawn to solving complex problems.
I also started my career doing statistical analysis, so I was interested in how you could apply that to this sector. How could we use more robust numerical or statistical models to optimize all aspects of production?
AFN: The last company you worked for (insect protein co AgriProtein) went into administration… what were the learnings you took from that?
JD: Some of it was about the history of that company and where they were in their journey. There was a mismatch between where they thought they were in terms of readiness to scale versus the reality. But I think there’s a broader sector issue with insect protein at industrial scale because the cost of hardware and energy can be very high to produce what is fundamentally a commodity: protein, although I think there are models of insect protein production that can work.
One thing that was fantastic about AgriProtein though, was that we were taking post-consumer food waste and processing that into the substrate for the insects, so our substrate was actually a source of income.
AFN: Moving onto shrimp farming! Let’s start with the basics about recirculating aquaculture systems (RAS)
JD: The reason for doing recirculating aquaculture versus coastal pond systems is that you eliminate externalities such as weather and disease.
For shrimp, what I saw when I was visiting farms all over the world was that they were managed in a very ad hoc way, there was a kind of pump and dump approach and general disregard for the environment, but the big problem were the externalities. No amount of optimization can overcome an extreme weather event such as a typhoon or a disease outbreak.
The big pathogen that emerged in 2012/13 [causing devastation in some parts of the shrimp farming industry] was EMS (early mortality syndrome), a bacterial pathogen, which is very hard to deal with because bacteria are naturally part of the ecosystem.
With global warming, there’s only going to be more of these threats as warmer temperatures encourage microbial growth, so it seemed to me eventually that the [traditional coastal pond] system was simply not going to be efficient enough to be profitable in the long run.
So that’s why I turned to recirculating aquaculture.
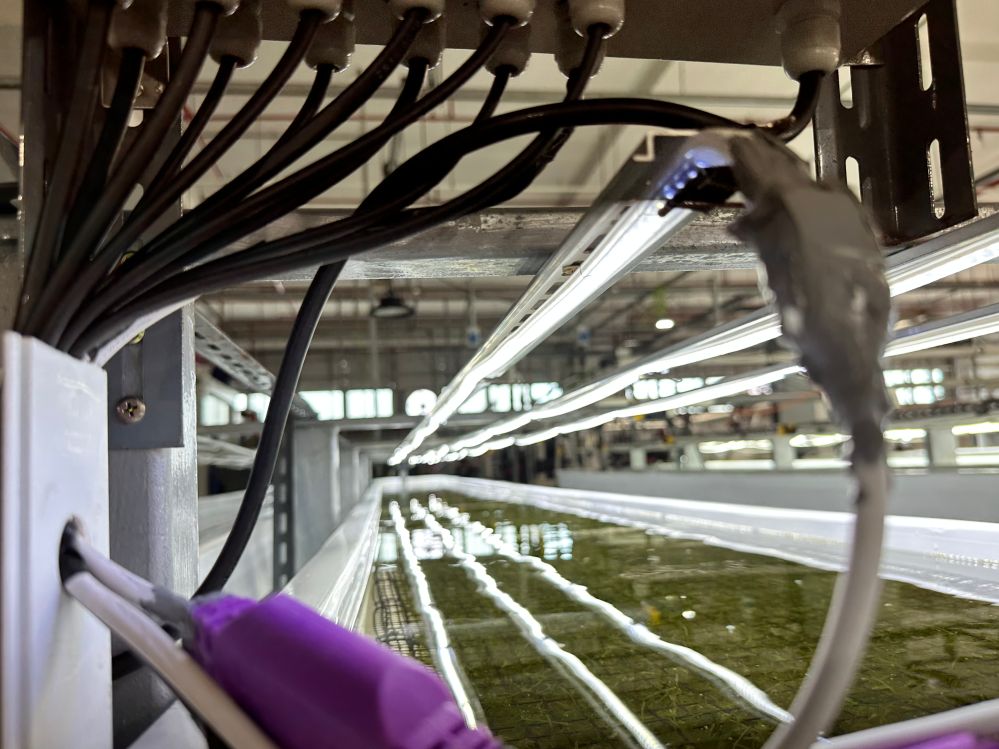
AFN: Which recirculating aquaculture system (RAS) is best and why?
JD: There are some basic variations of RAS systems. One is a biofloc system, where microbes are used to clear the waste, but the water ends up looking like thick soup and it’s impossible to determine what’s going on in your tanks, even with underwater cameras. You can also get off flavors from the biofloc.
But the bigger issue is that you’ve got this huge microbial community and those microbes need oxygen, so you’re using a lot of energy to dissolve oxygen into the water to support microbes, so in a way, you’re not growing shrimp, you’re growing microbes. And from an energy cost perspective, it’s not the most efficient.
The other [RAS system] is a clearwater system where you filter out the water using mechanical filters and then use disinfectants like ozone, which create byproducts that can potentially be problematic.
As I looked at these systems, I realized that they were not really optimized for maximizing productivity, which is a function of growth and density. So we ended up opting for a multitrophic model where we effectively recreate a natural ecosystem using macroalgae [seaweed] to take the ammonia and nitrogen out of the water.
The byproduct of shrimp metabolism of protein is ammonia, which above a certain level can be a negative growth factor or cause mortalities. So you want to minimize the amount that’s in the system. So we have a two-stage filtration system. The first step is using a mechanical filter to remove particulates, which can actually be used as a soil fertilizer.
But this filtered water still has dissolved organics in it like ammonia and phosphorus, so as a second step it then goes through a high-density algae multiplex with three different species of seaweed, which soak up all that nitrogen and phosphorus and everything else from the water so that the water going back to the shrimp tanks is polished of any of those nitrogen compounds.
Nitrogen is considered a waste in other systems, but in our system, it’s actually a fertilizer for the algae, which is also an income stream, although our unit economics are not dependent on that as a revenue stream.
AFN: What does your growing system look like at Vertical Oceans?
JD: In common RAS systems, you typically either round tanks or raceway tanks. The biggest difference at Vertical Oceans is that our tanks are designed to be movable, because if you want to maximize density, you have to be able to split the density of your tank periodically. As shrimp grow, the biomass density per unit area reaches the threshold where that density can become a negative growth factor.
Before you reach that threshold, you want to take a portion of the population out of a tank and put it into another one. That way, you’re able to start at a higher density, you reach a certain threshold, you reduce that population, that density goes down, you grow it up again, so we’re able to have five times higher biomass productivity per unit of tank area versus the next most efficient RAS system.
When you need to do a population split, you need to have another tank that’s proximate that you can split that population into, so by making the tanks movable [think of a warehouse racking system], you’re able to have a very dynamic way of always being able to split the density from the tank that’s critical into an empty tank.
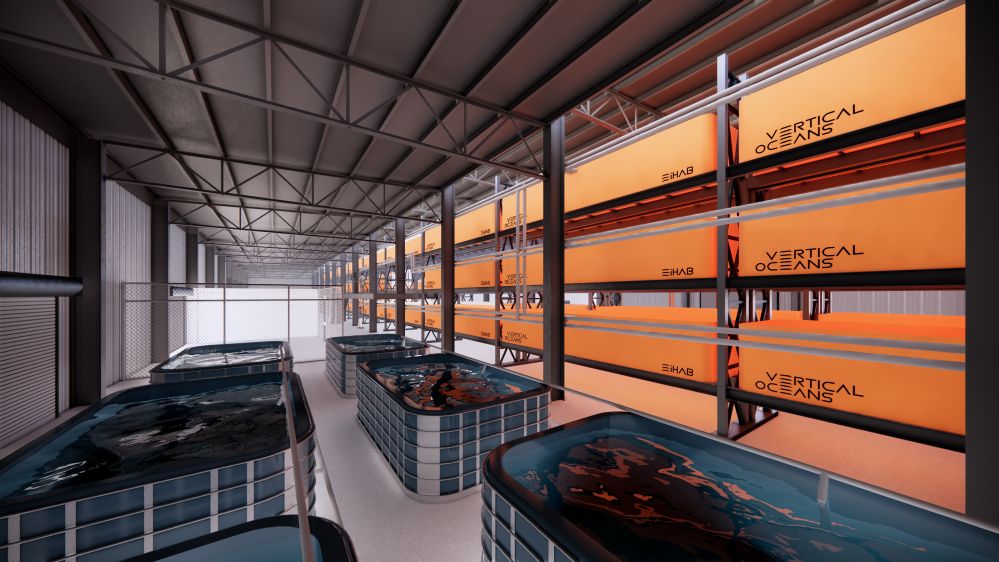
AFN: How are you transferring contents from one tank to another?
JD: There’s a special kind of pump that draws water in a very gentle way from one tank, goes through an inline counter, and then goes into the other tank, because we need to know exactly what population we’re transferring.
We bring the two tanks next to each other physically in what we call the pitstop, do the transfer, and then both of them go back into their resting bays. So it’s basically a racking system we call the aqua tower with a gantry robot in the middle that cantilevers the tanks in and out of their bay in the racking system.
In order to make that racking system spatially efficient, we had to make those tanks fully autonomous. Everything that they need to grow for that 10-15 day period of time is contained inside of what we call the lid module that’s on the top. All the equipment and feed are inside and everything is controlled by software.
Once the shrimp reach the harvest size, the gantry will bring the tank to the pitstop, we’ll harvest the shrimp, and then there’s a cleaning cycle before the tank receives a new population and goes back into the racking system.
AFN: Is all this tech off-the-shelf or proprietary?
JD: Almost all of it we’ve developed in house. For example, we needed a way of measuring the size and general condition of the shrimp [in the tanks] so we could calculate the biomass and so we had to develop our own underwater camera and computer vision systems. And then those feed into an algorithm that then determines how much feed to dose.
AFN: Where does the labor come in?
JD: We’re 99.4% autonomous, which is essential for the economics of a RAS production system to work. The only labor is really involved at the pitstop, to facilitate the transfer and a bit in the harvesting but that’s it. Ultimately, our ambition is that we would have zero labor required.
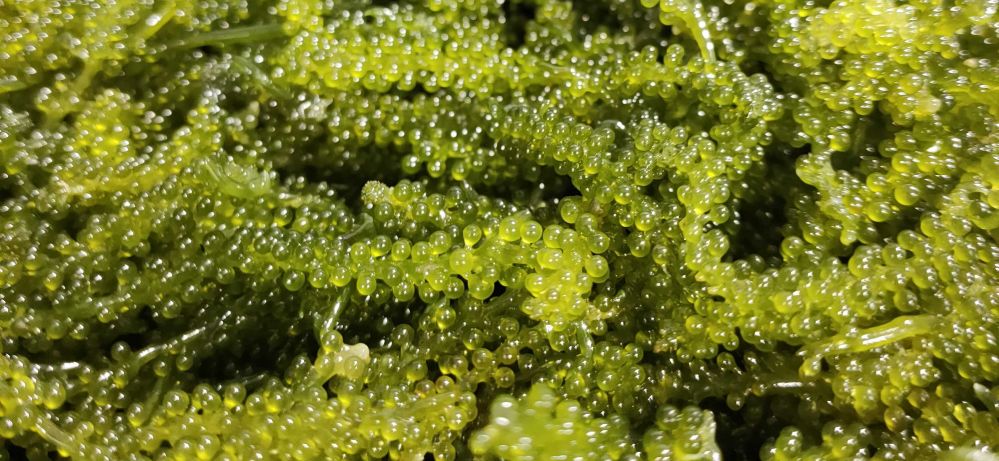
AFN: I understand that you’re doing some work on the microbes that live on the seaweed?
JD: What we didn’t realize is that algae are very microbially active, they have what’s called a holobiome, a complex community of microbes that live on the surface of the algae. And those microbes are producing a lot of metabolites from their natural processes that also have an impact on the water matrix and those microbes get introduced into the overall aquatic ecosystem.
So we have a third trophic level of these microbes. We’ve been doing metagenomics of our system for the last three years to profile that microbial community. And so now we have a blueprint of a healthy ecosystem and we can monitor how that ecosystem evolves over time. We also identified a couple of interesting microbes that we were able to isolate and we’re now producing those as part of a proprietary microbial inoculant.
And because of that microbial diversity, even though there are microbes that are potentially pathogenic to shrimp, we don’t see any pathogenic activity because those microbes are kept in check by all of the others that are in this system. And when they’re in balance those microbes are performing a valuable function in the overall ecosystem.
But we have worked hard to eliminate environments where negative bacteria could proliferate, so we don’t have any areas where there’s non-moving or stagnant water, so no settlement tanks.
AFN: Could EMS be a risk in your RAS system?
JD: Our shrimp are very healthy and we don’t see any pathology, but we know that having a greater diversity is a significant factor in creating and maintaining a healthy ecosystem. But once a month, we take a sample and we do the metagenomics on our system so that we can keep an eye on things
AFN: What’s the market for shrimp produced in this way?
JD: In the shrimp market you have same day fresh, never frozen premium product, where we’ve seen prices north of $30 a pound, and on the other hand, you have block frozen shrimp coming from coastal aquaculture ponds in Asia that can be as low as $5-7 per pound.
Our aim is to supply a better-quality product—our quality is on par with fresh wild-caught—but produced with production costs in line with frozen imported products, which will also enable us to compete in the mass market. So we’re having conversations with some retail chains about producing a frozen product that would be at a similar price or a little bit above traditional pond aquaculture, so we can play across that value chain.
One go-to-market model is to have Vertical Oceans that are approximate to major urban centers where a portion of the sales would be fresh to restaurants and retailers, and another portion would be frozen product that would be packaged under our brand for the frozen counter.
We’re also having discussions around having a much larger facility purely focused on frozen product that would be produced white label or under our own brand that would go into the frozen distribution chain of major US retailers.
AFN: Does the Vertical Oceans model work anywhere?
JD: It’s designed to be location agnostic. I visited a couple of RAS farms in the US, and one in Florida went bankrupt in part because they had so much energy cost associated with keeping the water warm.
I realized that in developing a system that’s location agnostic, the tanks have to be thermally efficient, so our tanks are fully enclosed and insulated, which makes them very thermally efficient. We just need a high bay warehouse and we can install our equipment in there. We also don’t need to be by any body of water as we are a zero-discharge recirculating system. We use less water than an average restaurant.
AFN: Are other RAS players adopting multitrophic systems?
JD: I see that some of them are starting to adopt a multitrophic approach, but we’re the only ones who have it proved out at scale. We’ve also been able to use the macroalgae growing system as a source of income, as one of the seaweed varieties we grow is Asparagopsis, which can be used for livestock methane reduction.
For example, we are working with one startup in this area and they are sending us the seed stock for the Asparagopsis and then they buy back the wet biomass from us. And because we have free fertilizer, basically [nitrogen and phosphorous from shrimp metabolism], and the cost of the algae is built into the cost of the shrimp, our marginal production cost is effectively zero.
And because there are those free fertilizers in the form of nitrogen and phosphorus, the seaweed grow really fast and we can produce quite a lot. One of the other species of algae that we grow can also be used as a food or feed ingredient, and we will add 2-3% of that into our shrimp feed, so we’re able to upcycle it back into the system.
AFN: How have you funded the business?
JD: I signed the lease for the proof-of-concept facility in late 2019, and in 2021, my cofounder Enzo Acerbi from AgriProtein joined me and we through the Indie Bio accelerator program.
Two thirds of the way through that, we were fortunate to have a term sheet from Khosla Ventures, so they led our $3.5 million seed round. And in early 2022, we moved from that little proof of concept facility into the facility we’re at now in Singapore, where we’re able to demonstrate all the technologies at relevant scale.
We’ve been producing and selling product for nearly three years now and we’re ready to build a larger facility, so we’re currently working on closing our series A round to finance that. It’s a challenge because no one is doing quite what we’re doing, as moving tanks is counterintuitive. In fact, it sounds kind of ludicrous.
But the technology isn’t really an issue. The biggest issue we have with investors is that they would like to see commercial validation of selling prices and so we’re having discussions with a number of distributors and retailers to get something on paper so that we can say, okay, this is the price that they’re willing to buy this product for.
When we talk to people in the industry, they get the value proposition right away. It’s fresh, locally-grown shrimp with no chemicals or antibiotics. It’s organic, easily traceable, it tastes really good, and it’s more sustainable. The fact that we can top them up with fresh product every single day means they can also eliminate shrink.
AFN: What’s your business model?
JD: We would envision owning and operating a certain number of facilities, as there’s a lot of gross margin there and it’s a good cash flow model. But we are also in discussions with business partners about a licensing arrangement, whereby the licensee owns and pays for the facility and we will design, install and commission it, train them on how to how to use it, provide ongoing technical support and maintenance of the AI software platform.
Another discussion that we’re having is about a much larger ‘Giga’ Vertical Oceans plant in the central US where production is dedicated to a few national retailers and one or two regional retailers for frozen product.
AFN: How do you minimize risk in your growing system?
JD: There are inherent risks in any biological system, but if one part of our system is compromised in any way, we can isolate it and take it offline, so we compartmentalize that risk. We are also very careful about what we allow into the system in the first place.
We have also developed microbial inoculants that we can introduce as a preventive measure if we see that we’re heading towards dysbiosis.