Ethanol producer Green Plains is gearing up to open a first-of-its-kind facility at a dry corn milling plant in Shenandoah, Iowa, that it claims will be able to produce dextrose at a commercial scale with significantly lower capital intensity and a 40% reduction in carbon footprint vs the standard wet milling process.
The facility is mechanically complete and in the commissioning phase, with shipments to customers beginning in the second quarter of 2024.
“We haven’t seen a new wet corn mill in the US for years,” Green Plains SVP Anand Sundaresan told AgFunderNews. “It’s just so capital intensive. We have a process [‘clean sugar technology,’ developed by subsidiary Fluid Quip Technologies] that can produce dextrose with a much lower carbon intensity and a much lower capital intensity.
“And we think it’s going to be truly disruptive, both to support the food industry [for bakery, confectionery etc] and for the growing bio-economy [dextrose is used as the primary feedstock for precision fermentation].”
Fluid Quip Technologies
One of the leading ethanol producers in the US, Green Plains has dry corn milling plants across the country and has been converting one of them at Shenandoah to deploy Fluid Quip’s clean sugar technology, whereby some of the corn grind is diverted into dextrose production, Sundaresan told AgFunderNews.
“Fluid Quip had two really innovative technologies. The first one, which we call MSC [Maximized Stillage Co-Products], can upgrade the protein that’s a byproduct of the ethanol production process in order to upscale it into what we call corn fermented protein, so it’s more bioavailable.
“The MSC system captures the yeast and the high-value corn protein from the whole stillage stream, resulting in 50%+ protein concentration, which is valuable for certain animal feed markets. So in the last three plus years, we invested a decent chunk of money to retrofit or add this technology which will enable the production of this protein.
“But the second technology, which is I believe is truly disruptive, is Fluid Quip’s clean sugar technology, which enables us to take some of the corn starch from the dry milling process and turn it into dextrose at a far lower capital intensity and carbon intensity than a wet corn mill, which is how all the big players [such as Cargill and ADM] make dextrose.”
“Clean sugar technology (CST) has the ability to upend traditional ethanol economics and increase margins significantly.” Green Plains Feb 2024 investor presentation
“We are rapidly negotiating commitments for dextrose from multiple strategic customers. The interest from parties across a variety of industries including food and beverage, yeasts, enzymes, biopolymers and biopesticides has exceeded our already high expectations. The demand for dextrose remains strong, and we expect to achieve food grade certification for this facility in the third quarter.” Todd Becker, CEO, Green Plains, May 3, 2024
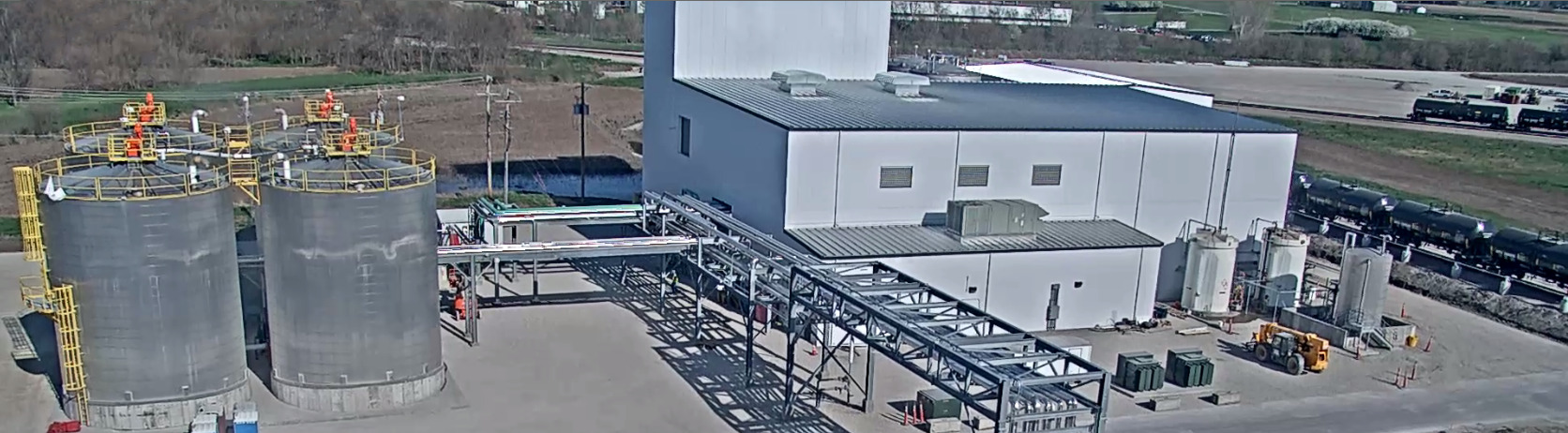
A simplified process
With a wet mill process, he explained, there is typically an initial steeping process followed by multiple grinding and separation processes (germ, fiber, gluten separation) followed by a starch liquefaction, saccharification, purification and evaporation process to get to dextrose. In its ‘clean sugar’ process, Green Plains cuts out many of these steps, going from grinding to liquefaction, fiber, oil and protein removal, saccharification, purification and evaporation.
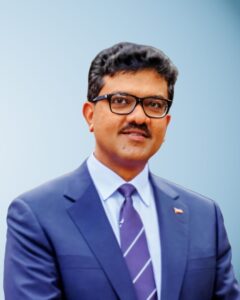
“The wet process is a lot more complex and capital intensive in terms of separating each fraction of corn into its constituent parts,” said Sundaresan. “The downside is that it requires multiple unit operations. We don’t have all these steps before we get to the starch. Once we liquefy the corn we basically remove the fiber, protein and oil via mechanical separation and then focus on breaking down the starch into simple sugars.
“We don’t end up with a corn gluten meal or a differentiated fiber stream [as you would from a wet milling process] but everything that’s removed goes back to the ethanol facility. So out of the plant you get ethanol, DDGS [distiller’s dried grains with solubles, the co-product of dry-milled ethanol production] and corn oil, which goes into renewable diesel. And if you deploy the clean sugar tech at an ethanol plant that also has the MSC technology, you’d also have corn fermented protein for animal feed.”
He added: “This is very exciting because it’s the first time this technology will operate at commercial scale. We’ll divert a percentage of the bushels of corn going to the ethanol plant, and we’re initially planning to produce over 200 million pounds of dextrose a year with the opportunity to expand to 500 million pounds.”
Food certification will take a few months, but industrial users will be able to use the product straightaway, he said.
“Ethanol demand is cyclical and volatile. It ebbs and wanes whereas the use of dextrose for fermentation or foods and beverages is less volatile, so that should lead to more consistent earnings for the company.”
Dextrose… with a 40% lower carbon footprint?
For buyers of dextrose, from biomanufacturing firms using it as a feedstock, to bakers and confectioners using it as a sweetener, the fact that Green Plains’ product has a 40% lower carbon footprint than dextrose produced by a wet corn milling plant is appealing as many companies have made commitments to lower their environmental footprint and cut scope 3 emissions.
He wouldn’t share details on pricing but noted that costs are lower. “We can convert the starch into dextrose at a much lower capital intensity.”